Originating in Japan, Lean methodology is a popular business management approach that focuses on maximizing customer value while minimizing waste. Specifically, it is a philosophy that aims to create more value for customers using fewer resources. In this article, we will delve into the principles, benefits, and applications of lean methodology.
5 key takeaways from this post:
- Lean methodology is a systematic approach to identifying and eliminating waste in all aspects of a business.
- The core principles of lean methodology are continuous improvement, value, flow, pull, and perfection.
- Lean methodology has many benefits for businesses of all sizes, including increased efficiency, improved quality, and increased customer satisfaction.
- Lean methodology can be applied to many different industries, including manufacturing, service industries, software development, construction, education, financial services, and healthcare.
- Lean methodology is often compared to Agile methodology, but the two approaches have some key differences, such as their focus, key principles, and project size.
The Origin of Lean Methodology
The origin of lean methodology can be traced back to the 1950s when Toyota, a Japanese car manufacturing company, was struggling to compete with the established American car companies.
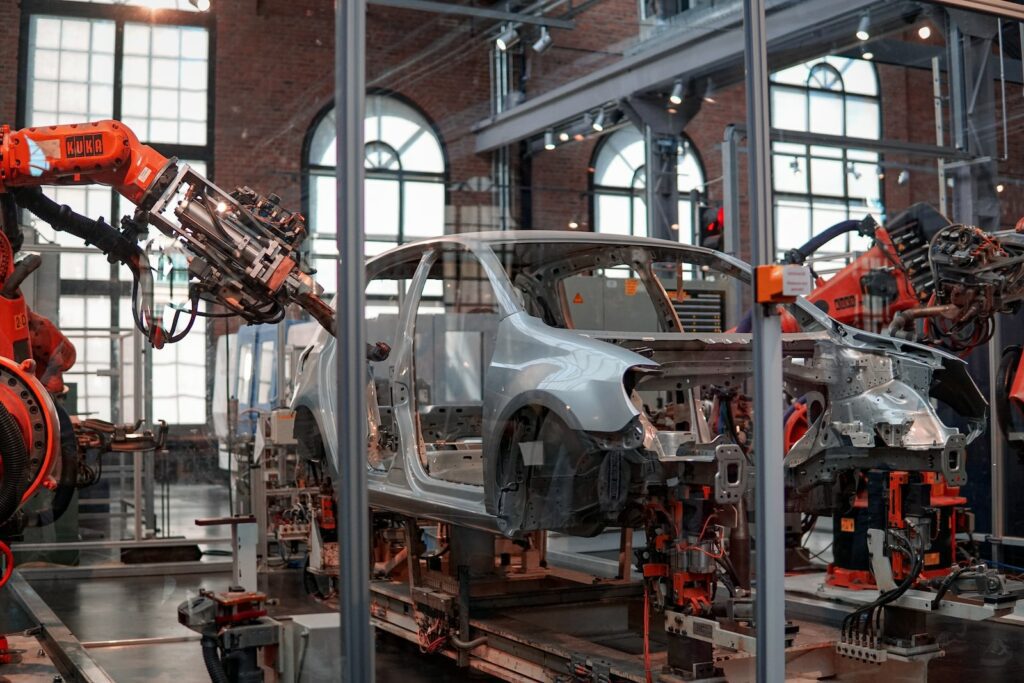
To improve their manufacturing processes, Toyota developed a new approach to business management that focused on maximizing efficiency and minimizing waste.
This approach allowed the company to create a system that delivered more value to customers with fewer resources. Toyota achieved this by focusing on continuous improvement, empowering employees to identify problems and find solutions, and creating a culture of excellence.
For example, workers on the factory floor were encouraged to stop the production line if they noticed a problem and were given the power to suggest improvements to the process.
As a result of this approach, Toyota was able to reduce waste in production, improve product quality, and ultimately gain a competitive advantage over their American rivals. The success of Toyota’s lean methodology didn’t go unnoticed, and soon other companies began to adopt this approach.
Today, lean methodology is used in industries all over the world, from manufacturing to service industries and even software development. Companies like Amazon and GE have used lean methodology to streamline their operations and improve their bottom line.
So, what exactly is lean methodology? Let’s take a look.
What is Lean Methodology?
Lean methodology is a systematic approach to identifying and eliminating waste in all aspects of a business.
The core principles of lean methodology are:
Continuous Improvement
Continuous improvement is at the heart of lean methodology. It is the process of constantly looking for ways to improve the efficiency and effectiveness of a business. This is achieved through a focus on the customer, reducing waste, and empowering employees to identify problems and find solutions.
One of the key tenets of continuous improvement is the concept of Kaizen. Kaizen is a Japanese word that means “change for the better” or “continuous improvement.” It is a philosophy that emphasizes the importance of making small, incremental changes to a business process to improve efficiency and reduce waste.
Value
The second principle of lean methodology is value. This principle focuses on understanding what the customer wants and needs, and then delivering that value in the most efficient way possible. By providing value to the customer, businesses can create long-term loyalty and increase profitability.
To understand customer value, businesses must engage in a process of continuous listening and learning. This involves gathering feedback from customers, analyzing that feedback, and making changes to the business process to better meet customer needs.
Flow
The third principle of lean methodology is flow. This principle focuses on the smooth flow of work through the organization. By eliminating bottlenecks and reducing delays, businesses can increase efficiency and reduce waste.
To achieve flow, businesses must engage in a process of value stream mapping. Value stream mapping is a tool that helps businesses to identify the steps in a process where value is added and where waste is created. By analyzing this information, businesses can identify ways to streamline the process and improve flow.
Pull
The fourth principle of lean methodology is pull. This principle focuses on ensuring that the right amount of work is done at the right time. By using a pull system, businesses can avoid overproduction and reduce waste.
A pull system is a system in which work is performed only when there is demand for it. This is in contrast to a push system, in which work is performed regardless of demand. By using a pull system, businesses can avoid overproduction, reduce inventory costs, and improve efficiency.
Perfection
The final principle of lean methodology is perfection. This principle focuses on striving for perfection in all aspects of the business. By constantly looking for ways to improve, businesses can achieve a competitive advantage and create long-term success.
To achieve perfection, businesses must engage in a process of continuous improvement. This involves identifying areas for improvement, implementing changes, and then measuring the impact of those changes. By engaging in this process of continuous improvement, businesses can create a culture of excellence and achieve long-term success.
Benefits of Lean Methodology
Lean methodology has many benefits for businesses of all sizes. Some of the most significant benefits include:
- Increased Efficiency: By eliminating waste and improving processes, businesses can significantly increase efficiency. This can lead to faster delivery times, reduced costs, and increased profitability.
- Improved Quality: Lean methodology focuses on delivering value to the customer. By understanding what the customer wants and needs, businesses can improve quality and increase customer satisfaction.
- Increased Flexibility: Lean methodology encourages businesses to be more flexible and responsive to change. By empowering employees to identify problems and find solutions, businesses can quickly adapt to changes in the market.
- Improved Employee Morale: By empowering employees and involving them in the continuous improvement process, businesses can improve employee morale and engagement. This can lead to a more positive work environment and increased employee retention.
- Increased Customer Satisfaction: By focusing on delivering value to the customer and improving quality, businesses can increase customer satisfaction. This can lead to increased customer loyalty, repeat business, and positive word-of-mouth referrals.
Lean vs Agile
Lean methodology is often compared to Agile methodology, but the two approaches have some key differences. While Agile focuses on delivering working software quickly and adapting to change, Lean focuses on delivering value to the customer and improving processes. Both methodologies can be used in software development, but Lean is often preferred for larger, more complex projects that require a more systematic approach to problem-solving.
Aspect | Lean Methodology | Agile Methodology |
---|---|---|
Focus | Delivering value to the customer, improving processes | Delivering working software quickly, adapting to change |
Key Principles | Continuous improvement, value, flow, pull, perfection | Individuals and interactions, working software, customer collaboration, responding to change |
Project Size | Larger, more complex projects | Smaller, more flexible projects |
Problem-solving | Systematic approach to problem-solving | Adapting to change and finding solutions quickly |
Tools | Value stream mapping, 5S, Kanban | Scrum, Kanban, Extreme Programming |
Application of Lean Methodology
Lean methodology can be applied to many different aspects of a business, including:
Manufacturing
Lean methodology was originally developed in the manufacturing industry. By improving processes and reducing waste, businesses can significantly increase efficiency and reduce costs. Common lean tools used in manufacturing include value stream mapping, 5S, and Kanban.
Service Industries
Lean methodology can also be applied to service industries, such as healthcare, hospitality, and retail. By improving processes and reducing waste, businesses can improve customer satisfaction and increase profitability. Common lean tools used in service industries include process mapping, visual management, and standard work.
Software Development
Lean methodology is increasingly being used in software development. By focusing on delivering value to the customer and empowering employees to identify problems and find solutions, businesses can improve the quality of their software and increase customer satisfaction. Common lean tools used in software development include Agile, Scrum, and Kanban.
Construction
Lean methodology can be applied to the construction industry to identify and eliminate waste in the building process. By using lean tools like value stream mapping and visual management, construction companies can increase efficiency and reduce costs thus improving cashflow in the construction businesses.
Education
Lean methodology can also be applied to the education industry to improve processes and reduce waste. By focusing on delivering value to students and empowering teachers to identify problems and find solutions, schools and universities can improve the quality of education and increase student satisfaction.
Financial Services
Lean methodology can be used in the financial services industry to improve processes and reduce waste in areas such as loan processing and customer service. By using lean tools like process mapping and standard work, financial institutions can increase efficiency and reduce costs while improving customer satisfaction.
Healthcare
Lean methodology can also be applied to healthcare to improve patient outcomes and reduce waste. By improving processes and identifying areas for improvement, healthcare organizations can increase efficiency and reduce costs. Common lean tools used in healthcare include process mapping, visual management, and standard work.
Tools to Implement Lean Method
Here are some tools to implement lean methodology in your business:
- Value Stream Mapping: A tool that helps you identify the steps in a process where value is added and where waste is created. By analyzing this information, you can identify ways to streamline the process and improve flow.
- 5S: A workplace organization method that involves sorting, simplifying, sweeping, standardizing, and self-discipline. This method can help you improve efficiency, reduce waste, and create a more organized and productive workplace.
- Kanban: A visual system that helps you manage workflow and inventory. By using a Kanban board, you can track the progress of tasks and identify bottlenecks in the process.
- Process Mapping: A tool that helps you identify the steps in a process and the inputs and outputs of each step. This can help you identify areas for improvement and eliminate waste.
- Visual Management: A system of visual cues that helps you manage workflow and identify problems. By using visual cues like color-coding and signage, you can improve communication and reduce errors in the process.
By using these tools, you can implement lean methodology in your business and improve efficiency, reduce waste, and create a more sustainable future for your organization.
Conclusion
In summary, lean methodology is a practical and effective way to manage your business operations. By prioritizing customer value, reducing waste, and empowering your employees, you can improve your business efficiency and profitability.
Regardless of your industry, implementing lean principles can help you achieve your goals and create a more sustainable future for your business. So, if you’re looking for a way to streamline your processes and improve your bottom line, lean methodology may be the solution you’re looking for.